P.J. Kortens: Industrial Control Solutions since 1987
We are an independent, instrumentation controls service and support organization with over 170+ years of combined experience. Serving Wisconsin, Illinois, and Northern Michigan, PJ Kortens & Co. delivers custom industrial control systems, PLC programming, and SCADA solutions that drive efficiency for industries like food processing, water, and wastewater. From concept to completion, we ensure seamless integration and unparalleled support.
Providing 24/7 on-call service, remote troubleshooting, and fast on-site support when needed.
Expertly designed industrial control panels following all UL508A and NEC code requirements.
A LONG TERM PARTNER
More than 35 years in operation
Since 1987, PJ Kortens & Co. has been delivering tailored control system solutions to help businesses optimize their operations and ensure reliable performance. With a deep understanding of complex industrial processes and a commitment to customer satisfaction, we bring decades of experience to every project. Our team’s longevity and technical expertise make us the trusted partner for automation solutions that stand the test of time.
Waste & water
Food & Dairy
& More
INDUSTRIES SERVED
We have a wide range of experience in Food & Dairy and Water/Waste water industries. We have also worked with clients in the Metals & Mining, Electrical Generation, Secondary Fiber, Paper, Distribution, and Chemical industries.
Proudly Serving Wisconsin, Michigan, and Illinois
A Trusted Partner for Midwest Municipalities
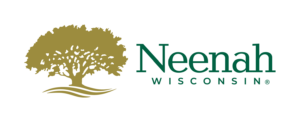
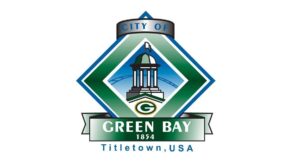
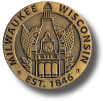
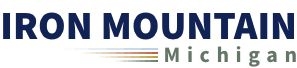

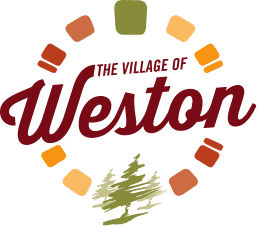
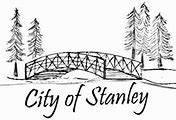
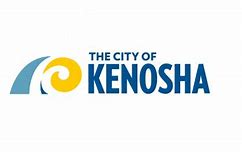
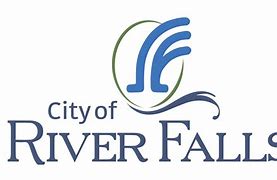
OUR MISSION
Our purpose is to deliver reliable, durable, effective industrial automation solutions to meet our customer’s needs.
OUR VALUES
Our people’s confidence, competence, and a dedication for excellence are the keys to our success. Our long term commitment to them is to provide a safe, secure and rewarding workplace with respect, honor and fairness to all.
OUR BUSINESS
Our business is customer
satisfaction with the fastest response times and best integration solutions.